Localization: How incubed IT helps robots understand where they are
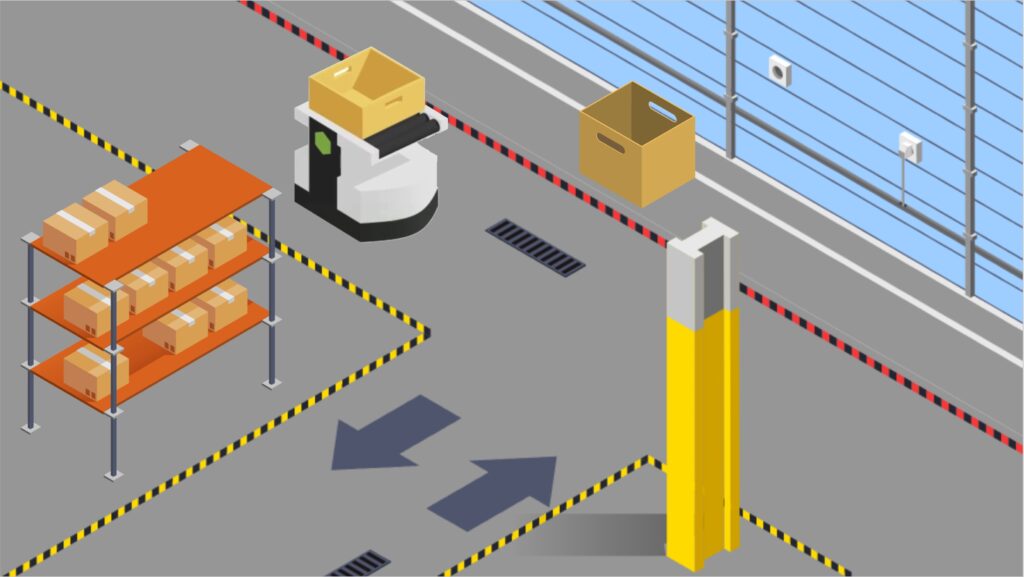
One of the key features that sets Autonomous Mobile Robots (AMRs) apart from other types of commercial robotics is their ability to navigate from point to point without pre-set paths. AMRs use sensors and software to intelligently calculate the best path and make adjustments as they avoid obstacles and accomplish jobs.
But in order to know where it needs to go, a robot needs to understand where it is located in the first place. At first glance, that might seem like a simple task — but it’s actually quite complicated. In an indoor environment, positioning needs to be extremely precise. Even a few centimeters off, and the robot might risk running into a shelf or failing to pick up a load.
That’s where localization comes in. Robotic localization is the ability for an AMR to understand its current position in regard to a coordinate system. The incubed IT software platform for AMRs includes localization algorithms that combine multiple measurements for the most accurate result.
Let’s dive into localization: how it works and why it matters for companies with robotics.
Human localization vs machine localization
Most travelers have experienced the disorientation of waking up in a hotel room away from home. Upon realizing you’re in an unfamiliar room, you begin to use all your available senses to determine where you are. Sight reveals the shape of the room, objects within it, and signage. Touch helps determine precisely how far away an object is. Sound and smell help you assess your environment.
All of this is quickly processed in the brain and compared to memories of other rooms you’ve been in. Within a few moments, you’ve oriented to your environment and remember where you are.
When a robot needs to orient itself to its environment, the process is comparable, but a bit different. Robots rely on inorganic sensors rather than human senses, and in place of brains they rely on software. This software interprets raw sensor data into useful location information and compares it to known locations.
It’s easier said than done. That’s why redundant location information is so important when helping AMRs localize on a factory floor.
The incubed IT localization software solution for AMRs
Der incubed IT software platform uses four technologies for AMR localization: coordinate system, odometer, particle filter, and laser scan matcher. A fusion of multiple algorithms improves accuracy so the AMR isn’t fully reliant on any one measurement.
Coordinate system
The coordinate system is the “map” onto which the AMR is placing itself. Similar to latitude and longitude lines, which indicate geographic coordinates on a globe, incubed IT uses a coordinate system to plot positions on a floor map of the facility in which the robot operates. This enables incubed IT software to visualize the robot’s location, and it supports the calculation of navigation paths.
Odometer
Most people are familiar with the odometer in your car, which keeps track of mileage driven over time. An AMR’s odometer is much more flexible. It tracks not only distance traveled, but also changes in orientation. This means you can map the path of an AMR as it travels, visualizing the robot during and after movement.
However, odometry alone isn’t sufficient for accurate localization because it includes errors which can add up over time. This can cause discrepancies between the calculated position of the robot and its actual position in the real world. The AMR needs to be able to initially orient itself, and then periodically reorient its position.
Laser scan matcher
A laser scan matcher uses lasers aboard the robot to scan objects in 360 degrees around the robot. It does this rapidly, often multiple times per second, and compares laser scans from one time stamp to another. Based on the changes between these laser scans, the algorithm calculates the motion of the robot.
For example, a robot may take an initial scan and find that there is an object five meters ahead.
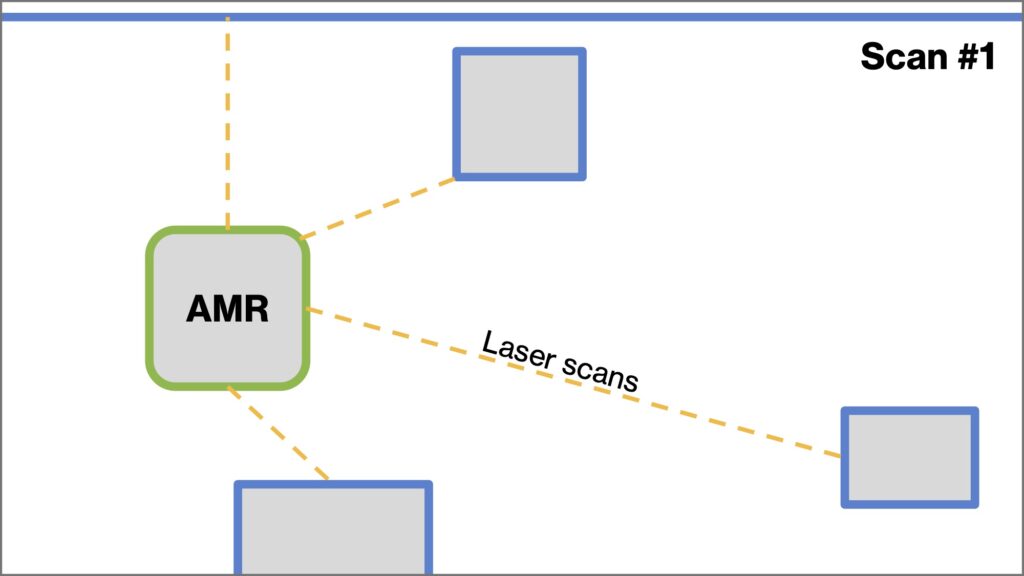
One second later, it may take a second scan and find that the object is now four meters away. (Note: laser scanners usually take readings multiple times per second. This example is simplified for easier explanation of the technology.)

The laser scan matcher would then calculate that the robot has moved one meter forward at a rate of one meter per second.
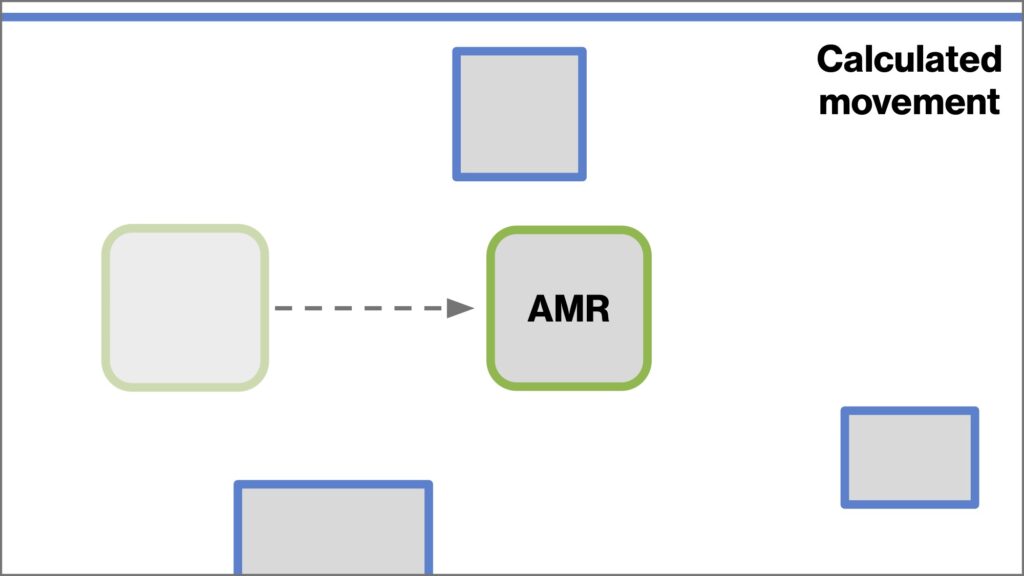
Of course, this measurement could be incorrect if the object ahead of the AMR is in motion — for example, if another robot is driving toward the first AMR. That’s why the AMR must scan the whole environment around it. It adds up the motion of the environment, determines which objects are stationary and which are moving, and then calculates the movement of the AMR itself.
However, laser scan matching can be faulty when used alone in an environment with too much motion. For example, an AMR positioned between two parallel assembly lines could mistake the moving assembly lines for a stationary environment, which might make the AMR calculate its motion to be faster or slower than reality. This makes comparison with odometer readings critical for accurate positioning.
Particle Filter
The particle filter is a second layer of information from laser scans. As laser scans are taken, the particle filter algorithm spreads digital “particles” — which are measurements of distances to objects seen by the AMR’s lasers — on a digital map of the facility in which the AMR is operating.
The particle filter algorithm gathers data from the laser scans, the motion of the AMR, and the base map, then calculates a probability score for each particle. As the robot moves, these probabilities can indicate what objects may be around the robot. This helps the AMR position itself in relation to known objects on the map: walls, pillars, shelves, and equipment. It also helps the AMR identify unknown objects and obstacles, such as a temporary stack of boxes, another robot, or a person walking by.
In addition to helping the AMR understand its own location, particle filter information plotted on the coordinate system map can also be shared between AMRs. Shared particle data helps robots maximize efficiency when navigating, since a robot can “see” obstacles ahead on the map before its own laser scans reach the object.
Why does localization matter?
The goal of implementing any AMR is to get a job done. To accomplish a task, the robot needs to navigate the space — and to do that, it first needs to know where it is. While it may not be the most exciting feature, localization is the first step toward more productive automation.
That’s why localization is an essential part of the incubed IT Robot Autonomy Platform, the software that goes onboard the AMR. Once again, the fusion of these localization technologies makes all the difference. While each system has potential for errors, incubed IT uses algorithms to cross-check the sensor data and minimize inaccuracies. It ensures that the robot is traveling along the correct path, rather than getting lost or de-localized.
Together with the incubed IT Fleet Management Server, the entire incubed IT platform enables powerful autonomy, greater control — and ultimately better work.
Want to learn more about incubed IT? Contact us at office@incubedit.com to set up a demo or ask questions.